Fabric finishes series: Mechanical
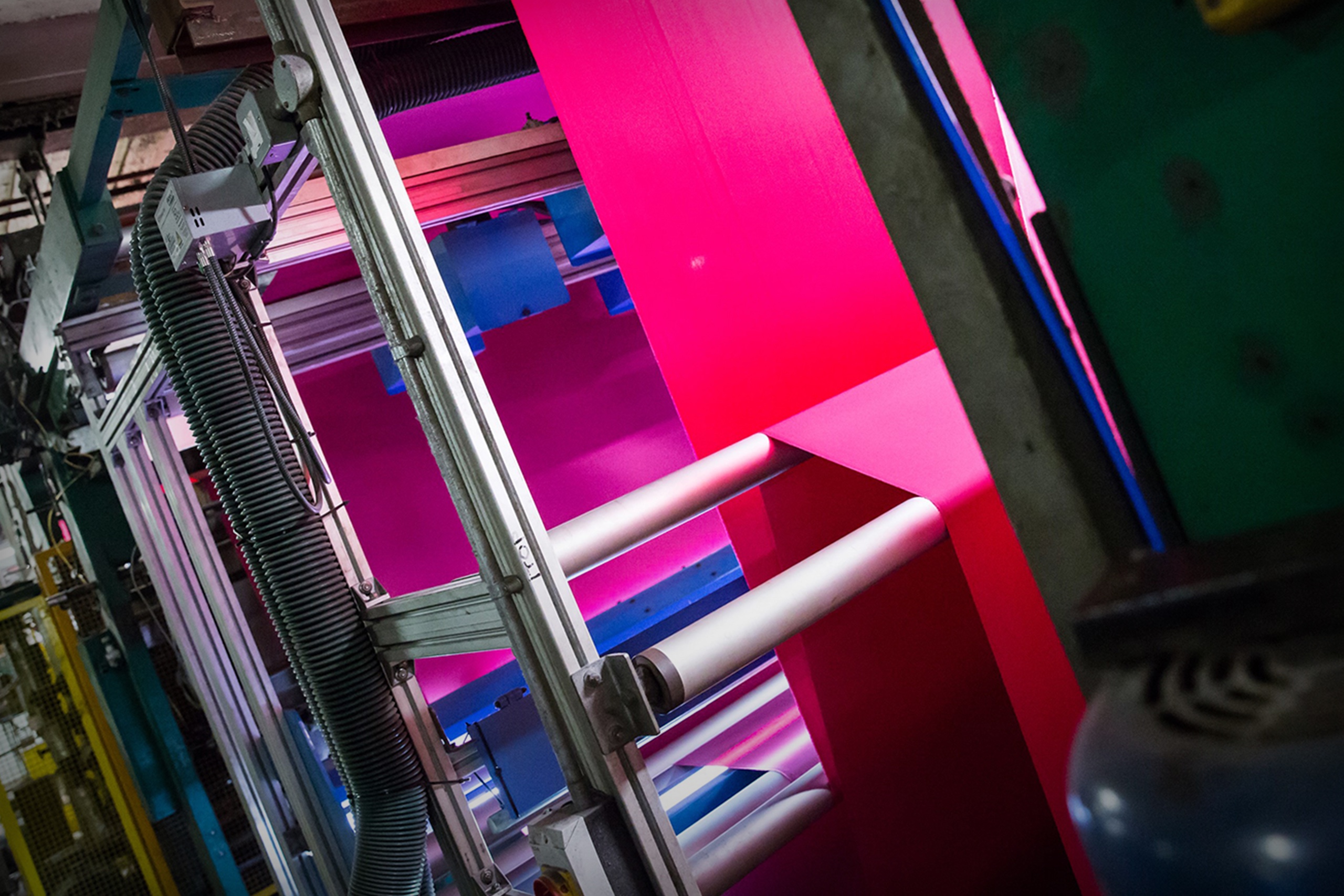
Textile manufacturers offer a range of fabric finishes to suit the needs of the end user in terms of appearance and performance.
In this second part of our textile finishing series, our Quality Assurance Manager, Sean Moore, focuses on the main mechanical fabric finishes available and their function.
“Mechanical finishing tends to happen on a stand-alone machine, some chemicals may be used such as lubricants used in raising and brushing but these are for aiding the process rather than imparting any additional attributes. Mechanical finishes are often used to enhance the design aesthetic as well as modify the performance.
Mechanical fabric finishes include:
- Sanforising / compaction: This is the most common type of mechanical finish. During processing the fabric is often stretched and if sold, as will in most cases, result in garments which shrink when washed. For example, people who bought jeans in the 50s or 60s had to put them on then sit in the bath and shrink them to fit. Sanforising (used on woven fabrics) or compaction (used on knits) compresses the fabric into a closer construction and thus reduces the amount of shrinkage which occurs. In the below diagram, the fabric is fed onto a rubber belt which is stretched over a roller, as the belt comes off the roller, it reduces in tension and therefore contracts, as it does so it starts to push the yarns in the fabric closer together.
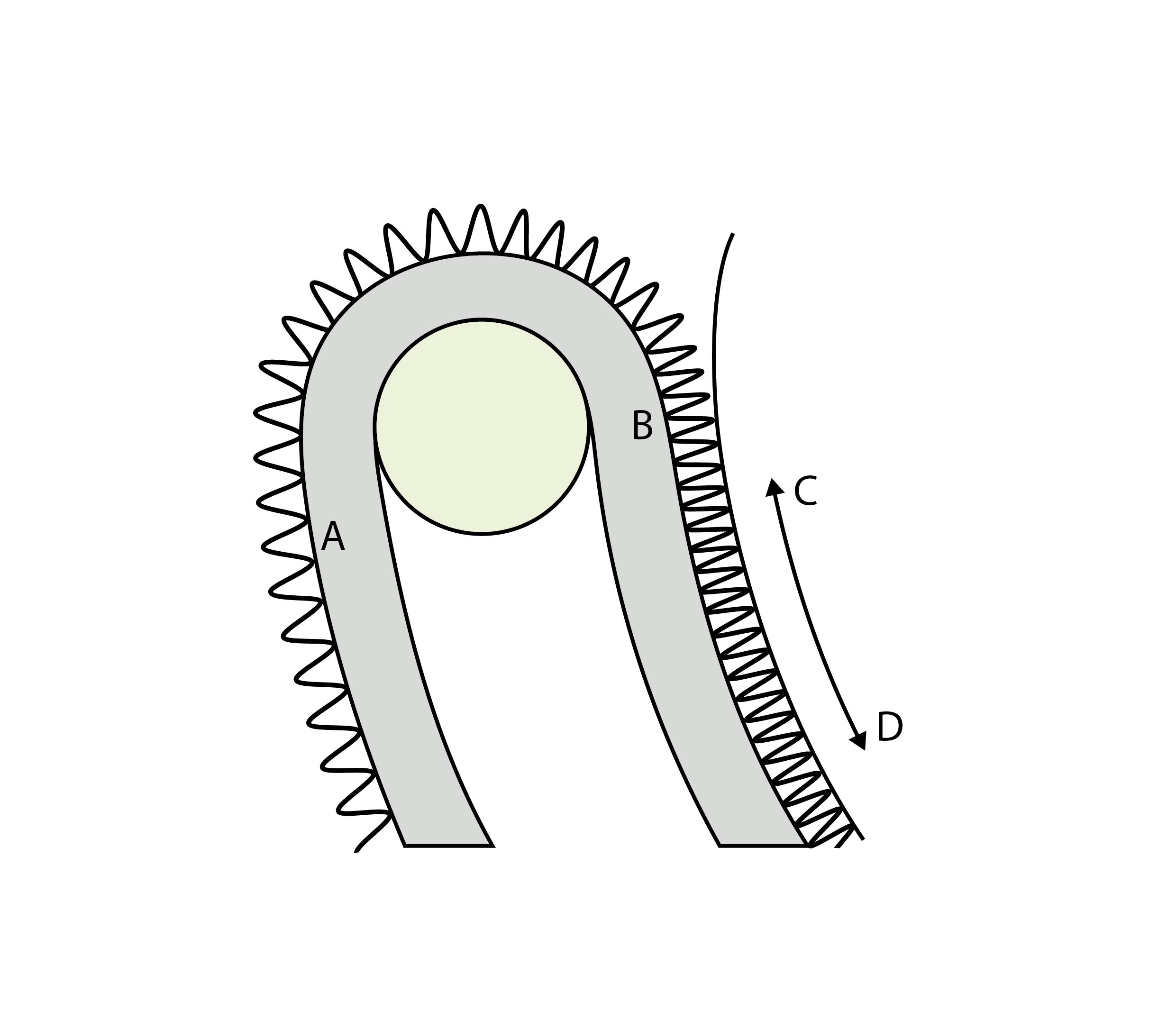
Sanforising / Compaction
- Raising / brushing: In raising the fabric is passed over a series of rollers which are covered with small upright wires, which tease out the individual fibres in the yarn and give a finish which is similar to a flannel cloth. Raised fabrics will also have a higher insulation value as the raised finish helps trap in air, an example of this would be the inside of hoodies which are often raised for warmth. Brushing is similar to raising but instead of using wires stiff nylon bristles are used. With brushing the effect is less pronounced than with raising. Fabrics must be carefully chosen to allow the fibres to pull free, if the yarns are too tight it’s possible that the brusher or raiser will have little effect.
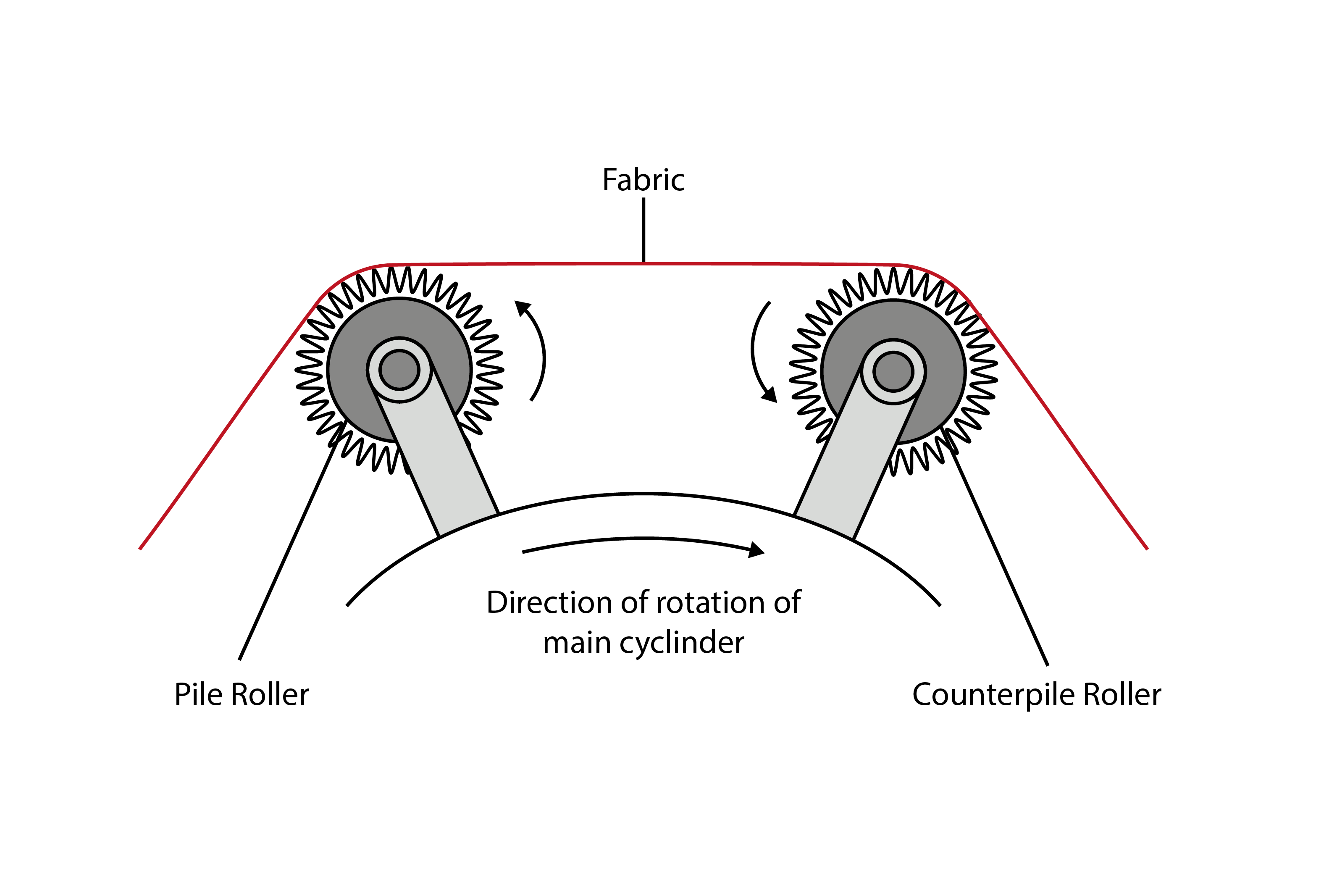
Raising / Brushing
- Emerising: For an emerised finish, sometimes called sueded or peach skin finish, fabrics are again passed over rollers but instead of wires or brushes these are covered with emery, a cloth which is an abradant. This lightly sands the surface of the fabric and raises a very fine level of fuzz. Most fabrics can be emerised, but care must be taken as the abradant can weaken the yarns.
- Calendering: Sometimes called Schreinering, is the process where the fabric is passed through two or more rollers, some of which are heated, and are pressed together under high pressure and the result is that the fabric becomes more compressed, smoother, and lustrous. Calenders can also be used to give a Chintz finish, which gives the fabric an overall sheen. Sometimes it’s possible to replace one of the smooth rollers with an engraved roller giving an embossed look to the fabric. Embossing a prepared fabric will cause the different parts of the fabric to dye differently so the result is a subtle tone-on-tone effect.
Plasma Fabric Finishing
There is a third type of finishing, which is energy or specifically plasma. Plasma has been around for several years but has seen a low uptake in general textile finishing and technically it is more of a booster process than a specific finish. The fabric is passed through a plasma field and depending on the type of finish the plasma can be used either to ablate/etch the surface of the fibres giving more sites for the finishing chemistry to latch on to, or the plasma raises the molecular charge of the fibre making it more attractive for the finishing chemistry. Mills using plasma have claimed that it has reduced their chemical use. So perhaps with the focus on sustainability we will see more plasma systems in use.