Flame retardant fabric terms, fibres, tests and norms
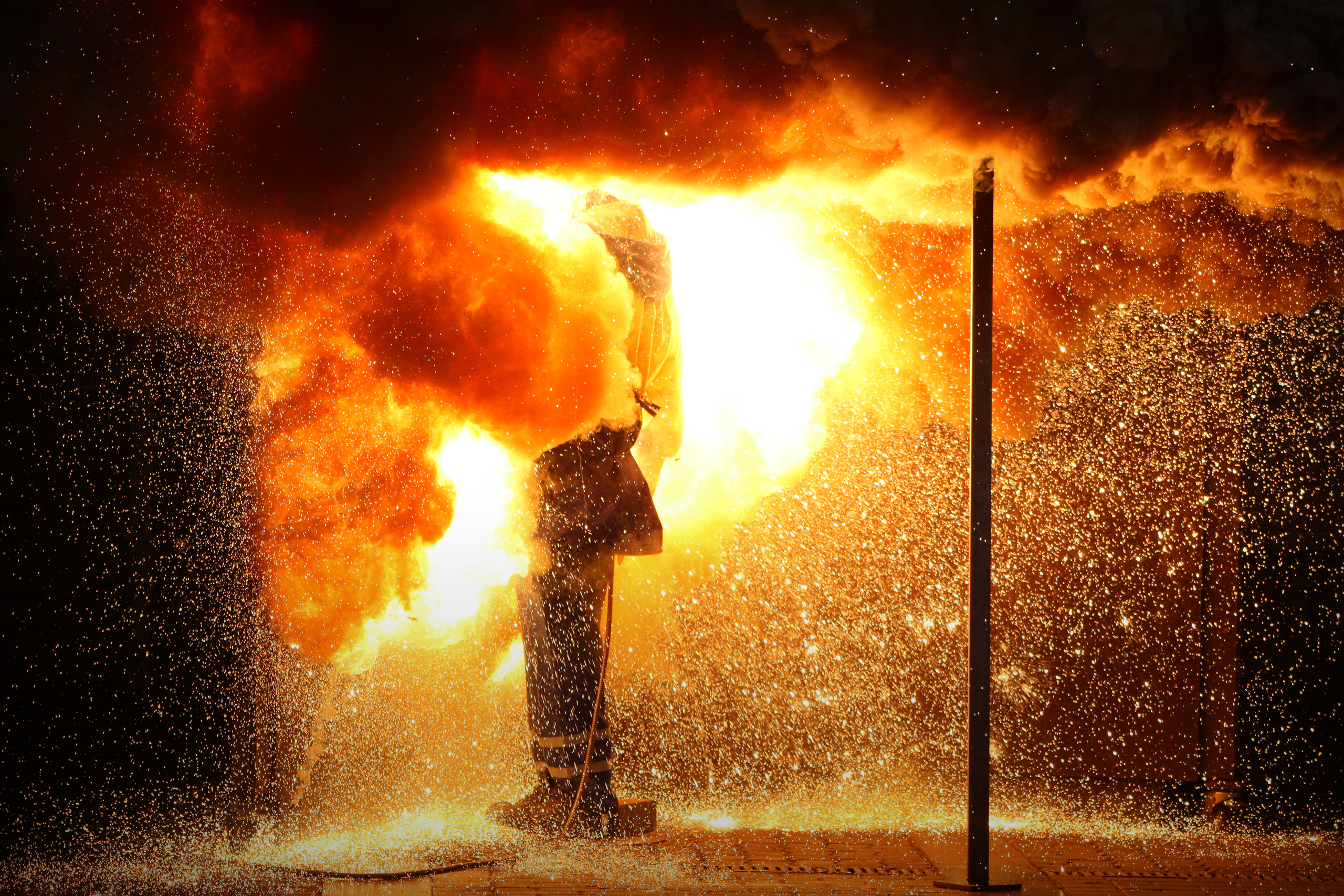
Why use flame retardant fabrics for workwear?
Normal fibres used in workwear garments such as polyester, cotton, viscose and nylon will catch fire if exposed to an ignition source and continue to burn after the ignition source has been removed.
FR fabrics and garments are designed to resist ignition, to prevent the spread of flame from the immediate area of exposure to the heat source and to self – extinguish either immediately or within a very short space of time after the heat source has been removed.
Common causes of ignition of workwear include electrical arc events, exposure to spark or spatter from welding, grinding, plasma cutting and other associated activities, ignition of flammable contamination on the garment, contact to or very close proximity to molten metal, flash fire or explosion of combustible dust.
PPE
The driving force behind the business of FR fabrics and garments in the EU is legislation. Any items sold in the EU are governed by the PPE Regulation (EU) 2016/425.
PPE can be broken down into 2 levels:
- Primary PPE: refers to clothing and items designed for use in work end uses where there will be significant exposure to heat, flame and or molten metal splash; for example foundry protection suit.
- Secondary PPE: refers to clothing and items designed for continuous wearing in work end uses where there is intermittent exposure to flame, heat and or molten metal splash, for example mechanic’s overalls. Secondary PPE is often worn under primary PPE. The majority of the FR PPE fabrics that Carrington Textiles manufacture end up in secondary PPE.
The protection offered by secondary PPE can be overcome if there is excessive exposure. As a supplier of fabrics for PPE if you are asked for a fabric for a particular end use, you can only offer guidance, it’s the job of the end-user to make a risk assessment of it for that working area.
Useful Terminology
Flame resistant: Fabric or garment which is difficult to ignite and will self-extinguish. The product may be treated with chemicals to give it this property or it may be inherent due to the components use in the manufacture of the fibres.
Flame retardant: If you are being particular about the terminology, flame retardant refers to the chemical used to give flame resistance. But people often say our fabrics are flame retardant.
Flame Proof: These are fibres that are unaffected by heat, e.g., glass, asbestos, carbon, ceramic, etc.
Stoll curve: This is a graph which has time and thermal energy plotted on it to measure at what point pain and or second-degree burns occur. Named after Alice Stoll, who along with Maria Chianta worked in the 1950s and 1960s burning themselves, sailors, pigs and rats to establish when pain and burns occurred in relation to the amount of heat used and length of exposure.
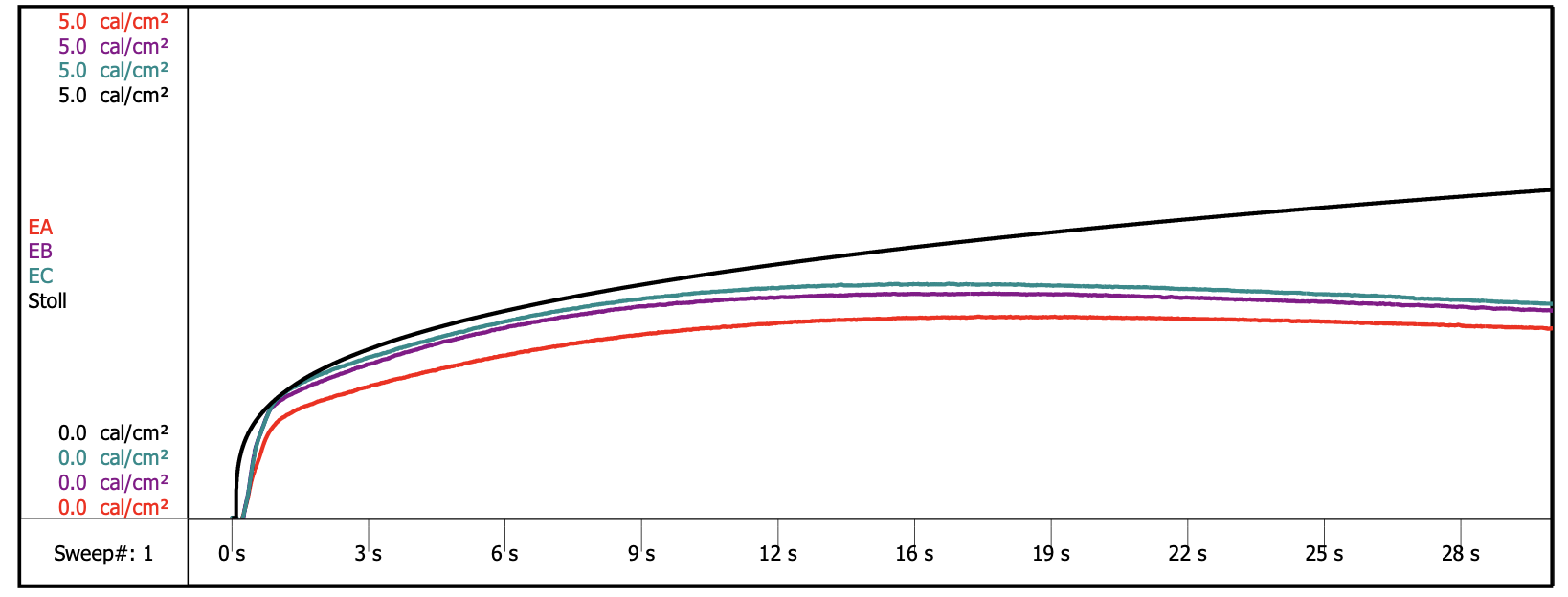
Stoll Curve
Flashfire: These occur in environments where fuel and air are mixed in adequate concentrations to combust, flash fires move rapidly and are typically less than 3 seconds. Garments are assessed for protection in the lab on a manikin, sometimes called the Thermo-man, although BTTG have called theirs Ralph (Research Aim Longer Protection from Heat). The manikin has several sensors which detect the heat rise and report, pain, 1st degree, 2nd degree and 3rd degree burns when the garment is exposed to an intense gas flame. Normally testing is done to 3 seconds, although some Aramid manufactures test to 4 seconds. The limit is 50% burns (excluding the head and hands). Test exists as ISO13506 and is also part of NFPA 2112.
Afterflame: The sample continues to burn after the ignition source is removed.
Afterglow: The sample continues to glow (like an ember) after the ignition source is removed. Normally if the afterglow stays in the already charred area, it is discounted but if the glowing spreads into the unburned fabric then the duration of the afterglow is measured.
Char length: This is not used in the EN ISO tests but the NFPA standards from the USA and the Russian standards ask for it. Basically, a gas flame is applied to the edge of a vertical fabric for a set number of seconds, and the length of the char caused is measured.
LOI: Stands for Limiting Oxygen Index. Air contains approximately 20% oxygen, it is possible for some FR fabrics to burn if the oxygen content of the atmosphere goes above the LOI of the fabric. For example, if you have a fabric with and LOI of 28 and the wearers are working in an atmosphere of 30% then it possible that the garments will still burn. Oxygen rich atmospheres are not normal workwear environments so it shouldn’t be worry.
Fire Tetrahedron / Fire Pyramid: The fire tetrahedron refers to the four aspects that are needed for a fire to burn, these are oxygen, fuel, heat/energy and a chemical chain reaction. If any one of these items is missing then sustained combustion is not possible.
The Difference Between Treated and Inherent
The easiest way to think of inherent is that the flame resistance is an intrinsic property of the fibre used to make inherent FR fabrics. Treated fabrics or fibres have had a chemical applied to them after the fibre or fabric has been produced.
There are several treatments on the market that offer no durability, these are not used or should not be used in workwear articles. Workwear articles need a level of durability, usually set by the supplier and can be as little as 5 domestic washes at 40°c or for the lifetime of the garment with industrial washing. There is no right or wrong fibre or fabric, each one will have certain properties.
To read more about the difference between treated and inherent FR fabrics read our article: https://hub.carrington.co.uk/resources/flame-retardant-fabrics-inherent-or-treated/
Common Fabric Tests
Arc test: This is where an electrical arc is created in a laboratory and sensors measure the amount of heat which passes through the fabric and if the Stoll curve is exceeded or not. Arc incidents can generate temperatures that are hotter than the surface of the sun, they give off large amounts of molten materials and the resulting sound waves can deafen workers permanently. Most of us will have seen an electrical arc at home when a light bulb blows, fortunately for us the breaker trips or the fuse blows, and the power is cut off.
The arc test can be broken down in to 2 types:
- EN 61482-1-2 Box test: This is favoured by the EU. In this test the laboratory causes an arc within an enclosure, this enclosure is open at one end so it focuses the arc energy out of this one opening, in front of which are the fabric/garment and the test sensors. It simulates a worker carrying out a task on switch gear. The test is subdivided into two energy ratings which are Class 1 where the arc is generated at 4kA (4,000 amps) or Class 2 at 7kA (7000 amps), the criteria is a pass or fail. most of our Carrington Textiles FR fabrics pass Class 1.
- EN 61482-1-1 Open arc: As the name suggests, in this test the arc is allowed to expand in 360°, three sensors are used to record the energy transmitted. In this test the arc is always made at 8kA, however it is held open for varying amounts of time so that the fabric can be assessed against different levels of energy. The old IEC version of this test gives the value in cal/cm² at which there is a 50% probability of 2nd degree burns. This will be the ATPV (Arc Thermal Protective Value) or the EBT (energy to break open). EBT is used as the senor only covers a small area of the fabric sample so it’s possible for part of the fabric to be destroyed and it is not picked up by the sensor so if this happens the EBT is reported. It has not been formally adopted in Europe due to the 50% prediction of burns but is used in the USA as ASTM F1959 the EN 61482-1-1:2019 uses a value called ELIM and this highest energy value at which there is 0% chance to burn.
EN ISO 14116: This is a basic standard, there are requirements for strength and also a limited flamespread test is carried out and there are three classes or indexes as they are called:
- Index 1: The flame does not spread, there are no flaming debris, no afterglow, a hole may be formed.
- Index 2: The flame does not spread, there are no flaming debris, no afterglow, no hole formation.
- Index 3: The flame does not spread, there are no flaming debris, no afterglow, no hole formation, the afterflame time of each individual specimen shall not be greater than 2 seconds.
For PPE, Index 3 is the requirement.
EN ISO 11612: This norm covers workers exposed to heat and flame. It’s subdivided into a set of physical requirements, e.g., shrinkage, tear, etc. that are mandatory. The fabric must then pass the limited flamespread test at the same level as EN 14116 index 3 for face (Class A1) and or edge (Class A2) ignition, it must then also pass at least one of the following Exposure to Convective Heat (Class B) Radiant Heat (Class C), Molten Aluminium (Class D) Molten Iron (Class E) and Contact Heat (Class F), there is also an optional requirement for a flash fire test done on a manikin.
Classes A1 and A2 are pass or fail, classes B, C, D, E & F are divided into 3 performance levels.
EN ISO 11611: This norm covers welders’ clothing, the requirements are spilt into two classes, Class 1 for light duty welding and Class 2 for heavy duty welding. Like EN11612 there are some physical tests that the fabric must pass as well as limited flame spread, radiant heat and welding droplets test.
NFPA 2112: This is a USA standard, its full title is „NFPA 2112 Standard on Flame-Resistant Clothing for Protection of Industrial Personnel Against Short-Duration Thermal Exposures from Fire”. Like the EN ISOs above the standard is split into a set of requirements, there is a flamespread test which is applied to the edge of the fabric when its new and after 100 washes, this test also includes a char length requirement. There are requirements for heat transfer and heat resistance. Whereas the Flashfire Manikin test is optional in EN ISO 11612, its mandatory in NFPA 2112. The standard also includes requirements on 3rd party certification and even how the certification body should carry out their audits.
NFPA 70e: This is a USA standard for electrical safety in the workplace. It covers a whole host of safety requirements (120 pages) and section 130.7(c)(14) directs you to ASTM 1506 Standard Performance Specification for Flame Resistant and Electric Arc Rated Protective Clothing Worn by Workers Exposed to Flames and Electric Arcs. Similar to the EN ISOs there are requirements for strength and shrinkage. The limited flamespread test is an edge test with char requirements on new and after 25 washes, the lab should also report the weight of the fabric test and also the colour fastness. Finally they have to test the fabric for arc flash protection using ASTM F1959 (See open arc section on page 5).