Introduction to flame retardant fabrics
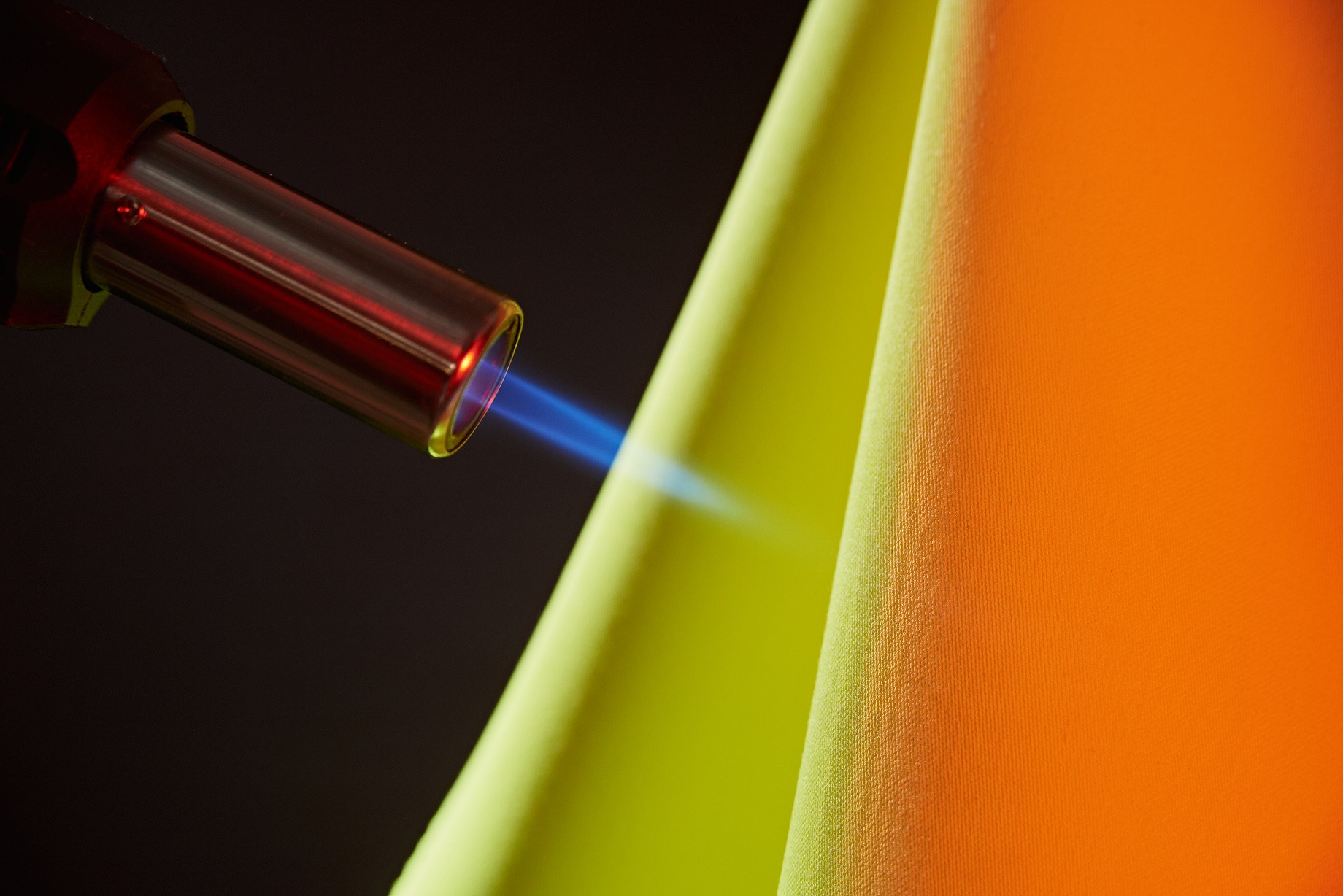
By Sean Moore: “Flame retardant fabrics for workwear can be a highly technical subject, but in this article, we simplify the basics on what types of FR fabrics there are and how they protect the wearer.
To start the process, let’s explain what is fire?
By definition, fire is a process involving rapid oxidation at elevated temperatures accompanied by the evolution of heated gaseous products of combustion, and the emission of visible (light) and invisible radiation (heat).
Oxidation is happening all around us, the coins in our pockets tarnishing, scratches on our cars going rusty, it’s even happening in our own bodies as our cells metabolise or we face oxidative stress through pollution than can make our skin age and wrinkle, the keyword in the definition above is ‘rapid’.
Traditionally people would discuss the fire triangle. As the name suggests it consists of three ‘legs’: Oxygen, Fuel and Heat (and sometimes Energy). If one of these ‘legs’ is removed fire cannot happen. Think of a candle, if you put water on a candle, it cools the flame so the candle goes out. Similarly, if you put a jar over the top of the candle provided no air can get in, the candle will go out once the air in the jar is consumed. Finally, if the candle is allowed to burn to the base all the fuel will be consumed, and the flame will extinguish.However, more research into fire has shown that there is a fourth element, which is a chain reaction. Once ignition has occurred the resulting chain reaction helps to sustain the combustion process. The triangle now becomes something called the ‘Fire Pyramid’ or ‘Fire Tetrahedron’.
In the chain reaction the ignition source heats up the oxygen in the air around the fuel making it more reactive, it also causes the fuel to decompose/break down and release volatile gases. These mix with the reactive oxygen to form radicals which then ignite and burn feeds heat energy back into the fuel and air and the chain reaction progresses.
Flame Retardant Fabric Types
Okay, so we now understand a little about fire or the combustion process. Let’s start to look at the FR fabric types.
What does FR mean? This is often a catch-all that’s used to cover both Flame Resistant (a general property of the fibre) and Flame Retardant (something has been added). There are also products that are Flame Proof such as glass, carbon and metalised fabrics, but these aren’t covered in this article.
You may also hear terms such as inherent and treated FR fabrics.
Inherent is used when the fibre has FR properties either by the nature of the fibre or because an additive has been put in at manufacturing stage.
Treated is used when a finish has been applied to the fabric. Treated is our biggest range of flame retardant fabrics for workwear at Carrington Textiles. We take the cotton/ cotton-based fabric and apply a finish that modifies the way the fabric burns or actually does not burn. I know there’s lots of debate on if inherent is better than treated but if a treated article is finished correctly and looked after in washing there is no reason why the FR will not last the life of the garment. Read our full article on this debate here.
How do flame retardant fabrics work?
Let’s move on to the mechanism of action, generally, there are 3 classes of action, and these are thermally stable, radical scavenging / disrupting and char forming.
Thermally stable:
- These FR fabrics fall under the flame resistant heading.
- They are fibres that don’t decompose below 400°c, so they don’t feed the chain reaction. (it’s possible to get some thermally stable fibres to burn but the oxygen content of the air needs to be much higher than naturally occurs).
- Because they don’t degrade with heat, they are common in end uses where extreme heat can be expected, e.g., firefighter turn out gear.
- They contain no fire retardant additives.
- In our sector the most common is the meta and para-aramids. There is also Kermel and PBI.
- These fibre types tend to be the most expensive.
Radical scavenging / disrupting:
- These fibres have an additive (so are flame retardant) and when they decompose, they scavenge or disrupt the formation of the radicals.
- The additive may be as a coating on the fabric (more common in furniture than PPE) or put in at fibre production stage (modacrylic).
- Mostly halogen based using bromine or chlorine (halogen and brominated systems are being phased out).
- Modacrylic is the usual fibre that we see in FR PPE.
Char forming:
- These are Flame Retardant fabrics that have had a chemical added either as a topical finish or during fibre manufacture, causing the fabric to decompose to a char. The char is formed at a lower temperature than is required to ignite the fabric and thus reduces the production of volatile gases.
- The char also acts as an insulating layer to give workers extra time to get themselves away from the heat source.
- The chemical used in char forming products is Phosphorus based.
- The systems can be non-durable, semi-durable or durable, (for PPE it must be durable).
- FR treated cotton has the largest volume in the market for flame retardant fabrics.
- It’s the cheapest option.
- It can be degraded if not washed correctly, however, if washed correctly it can last the lifetime of the garment.
To summarise, combustion (fire) is a complex chemical reaction. By breaking one of the legs of the ‘Fire Tetrahedron’ the combustion will be stopped.
In Fabrics for FR workwear there are three systems: thermally stable, radical disruptors and char formers.
Each system has its pros and cons and developers may choose to mix fibres and chemistries to optimise the end product.
Irrespective of if the system is an intrinsic property of the fibre or a chemical additive, it’s possible to create an FR fabric that is durable for the life of the garment. But they should not be viewed as ‘suits of armour’ any flame retardant PPE should be viewed as secondary protection and not used in place of good working practises.”
Sean Moore is Carrington Textiles’ Quality Assurance Manager. During Sean’s 32 years’ experience in the industry, he has developed some of the most successful testing and quality projects for some of the biggest textile companies in Europe.