The rise of EVs and antistatic fabrics for workwear
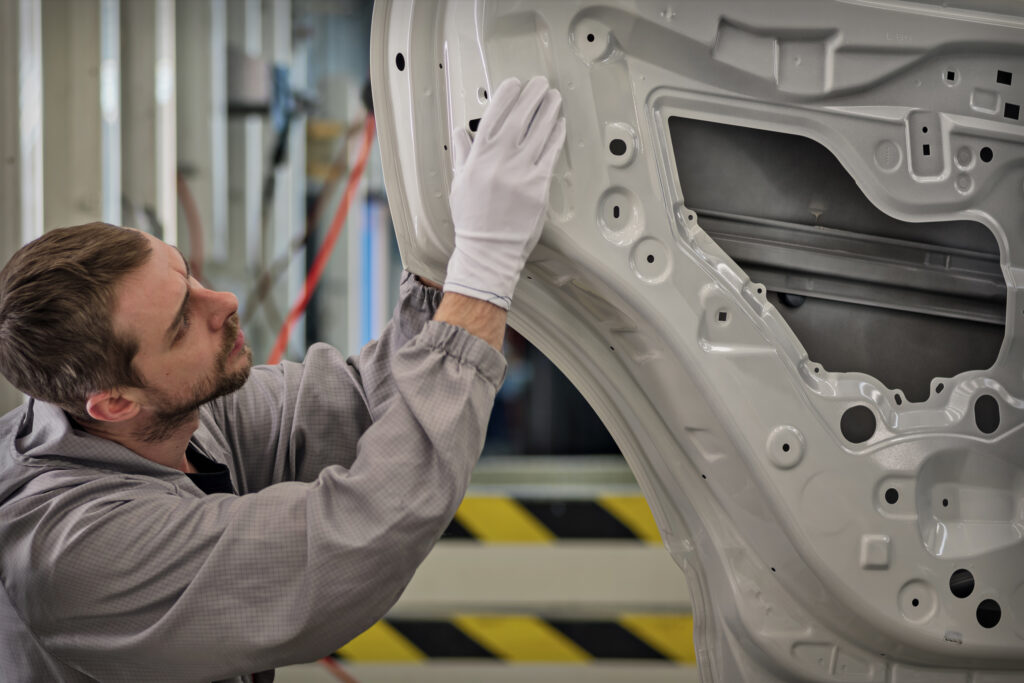
QA Manager Sean Moore: “More and more electric vehicles (EVs) are being manufactured and used on the roads these days. This brings with it challenges not only on how these cars and their components are produced, but also repaired. These challenges are similarly transferred across to the clothing worn by the assembly line personnel and mechanics working on these vehicles, who need uniforms made with antistatic fabrics.
“Typical workwear for a mechanic in car manufacturing may consist of a polycotton overall or trousers and a polo shirt, which is protective enough for fossil-fueled cars. However, EVs contain a myriad of sensitive electronic equipment. The battery pack itself is highly prone to static damage during manufacture, assembly and installation into the car, which in extreme cases can lead to an incendiary discharge or a battery fire.
“A major source of static discharge onto sensitive EV components and the battery is from the clothing worn during both manufacture and assembly. To provide full protection against the risk and consequences of a static discharge, antistatic fabric made workwear is considered an essential part of any hazard/risk assessment and cost-effectiveness studies in electric vehicle manufacturing.
The EN 1149-5 standard was designed to define antistatic fabrics performance
“To define the antistatic performance of any garment worn in both car and battery manufacture and assembly, the defining performance of the antistatic fabric is to EN 1149-5. This standard has been designed specifically to define the end-use performance in industrial areas such as electric car manufacturing where static can be a hazard to the vehicle components. In effect, garments made from fabrics meeting EN 1149-5 cannot cause a static discharge provided they are grounded. For PPE garments worn in areas of potential static risk where CE/CA marking is required, it’s mandatory that the fabric performs to EN 1149-5 for protection to the wearer.
“In an industrial environment like car and battery manufacture, it’s not possible to fully ground the person at all times, and this does present some potential risks to static discharge where surface conducting antistatic yarns are used in the fabric. However, the potential risk can be minimized by incorporating specific core conducting yarns that provide optimum protection even in ungrounded situations.
“Certain parts of battery assembly do present a risk of a life current discharge that can, itself, be triggered by a static discharge. In this specific area it is essential that the fabric and the garment also perform to EN 50286”.
Sean Moore is Carrington Textiles’ Quality Assurance Manager. During Sean’s 32 years’ experience in the industry, Sean has developed some of the most successful testing and quality projects for a few of the biggest textile companies in Europe.
Whether it is antistatic fabrics for workwear, flame retardant or waterproof garments, visit our website to find our wide range of antistatic products.