Fabric finishes series: Chemical
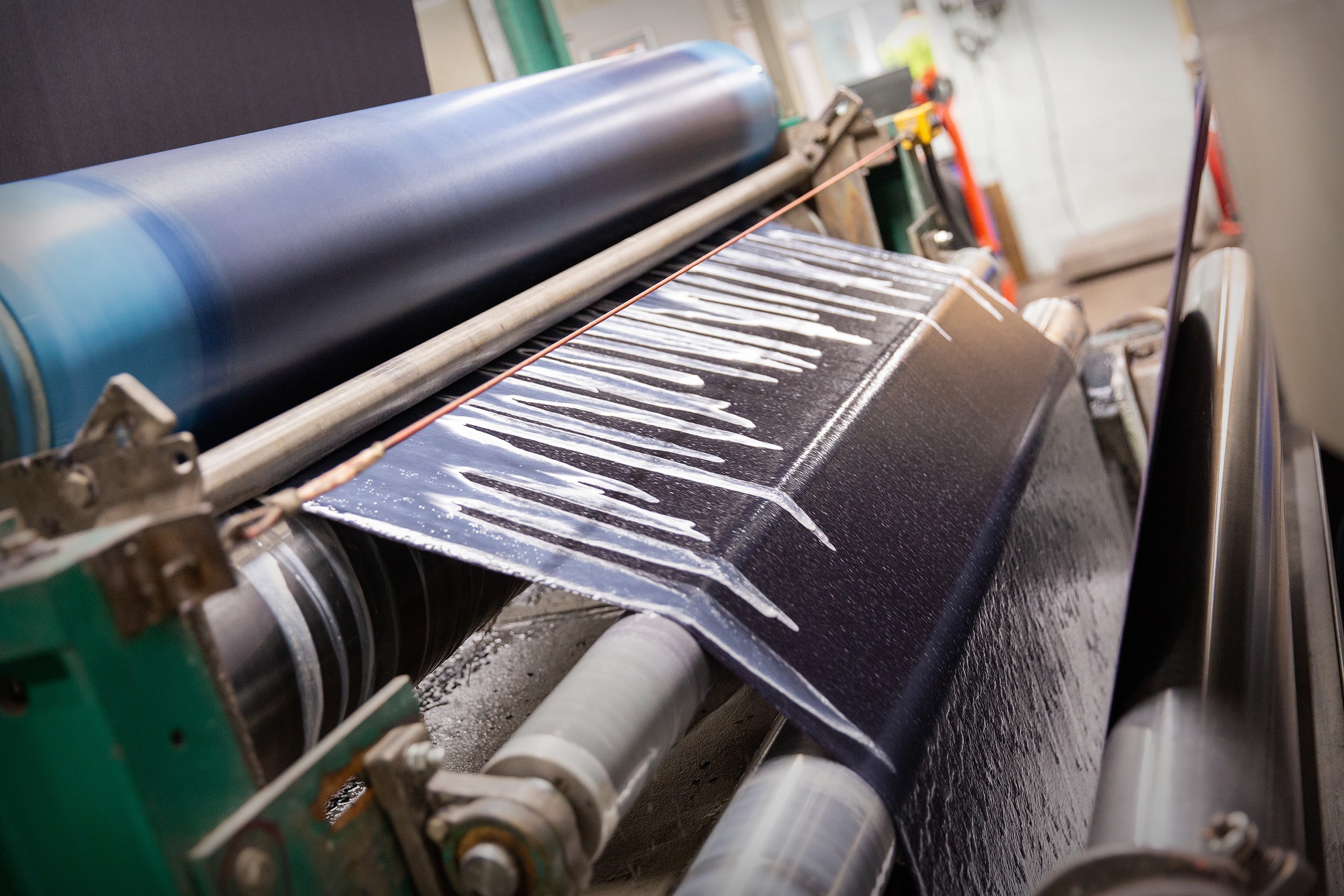
Manufacturers offering textile services offer a range of fabric finishes to suit the needs of the end user in terms of protection, comfort and performance.
These finishes are divided into chemical and mechanical. In this article, our Quality Assurance Manager, Sean Moore, focuses on the main chemical fabric finishes available and their function:
“As the name suggests chemical finishes use one or more chemicals to impart a performance aspect to the fabric that it does not yet possess.
When applying a chemical finish it’s important to consider not only the desired performance required but also any unwanted side effects. For example, some finishes will significantly reduce the strength of the fabric; a fabric which is soft may have a nice handle, but it may also increase the risk of pilling. It’s also important to consider if the chemical is compatible with the fibre type, for instance, the resin used on cotton will have no effect on polyester or nylon.
Most chemical finishes will be applied in a stenter pad, and these include:
- Crease Resist / Easy Care / Non-Iron: Resins are applied through a stenter, these cross-link with the cotton fibres to minimise the degree of creasing and thus lowering the amount of aftercare needed post-washing.
- Binders: Spun fabrics are made from short hairs and therefore may have a tendency to pill. By applying a binder, it’s possible to glue these hairs down and thus reduce the amount of pilling (bobbling). Care must be taken not to apply too much binder as the fabric will become harsh, stiff, and uncomfortable.
- Softeners: As the name suggests their aim is to make the fabric softer so a simple fatty acid or polyethylene product may be used which has two effects. One will slightly soften the fabric, the other provides stitch lubricant which minimises issues during garment make-up. If a very soft and drapey fabric is required then a silicone-based softener would be the best option, however, the end user will need to compromise on pilling.
- Soil release: To allow garments to be cleaned thoroughly, a soil-release product may be used. One way this will work is by allowing the fabric to absorb more water (wetting out) during the wash, where the water will dissolve any water-soluble soiling which is rinsed off. Another way this works is when a layer is formed on the surface of the fabric and the chemical is attracted to oils and greases allowing them to bind to the chemical rather than the fabric. During the wash, the outer layer of soil release (at a molecular level) is shed carrying away the oily soil from the garment.
- Water and Oil Repellency: Depending on the end use and performance requirements, something simple like wax can be used to impart water-repellence to fabric, and there is a whole host of new products based on natural chemicals/bioproducts being introduced due to the need for increased sustainability. These chemicals are often classed as C0 (C Zero) or PFC free. Unfortunately, due to the laws of physics, these finishes, whilst imparting water-repellency, have no oil repellency. Where oil and or chemical repellency is needed fluorocarbons must be used. The current fluorocarbon used in textile finishing is C6 and whilst this is more environmentally friendly than its forerunners C8 or Scotchguard, it still contains PFAS chemistry. PFAS chemistry will soon come under increasing legislation in the EU which will restrict its use to only very specialised end uses. Some US states have banned PFAS outright.
- Flame Retardants: Fibres such as cotton are not flame-retardant, however by applying the correct fabric finishes and curing them so they are permanently fixed into the fabric it is possible to create a cotton fabric which does not burn. Carrington Textiles uses a phosphorus-based chemical, under the presence of a flame the phosphorus caused the cotton fibre to degrade to a char before it gets the chance to ignite, see our Knowledge Hub article on FR fabrics for more information.
- Antimicrobial Finishes: During 2020 these finishes came under increasing scrutiny with the hope that they would reduce the spread of the virus. Whilst some types did confer antiviral properties others did not and there was not a great uptake of these products. Some of the products are based on silver, either ions or pure silver. Silver was found in Roman times to be anti-bacterial and may be the reason why the phrase born with a silver spoon in your mouth was coined as it showed that the well-born had better survivability. Some are based on quat salts, these are chemicals which have a high molecular charge, this acts as a sword and punctures the bacteria’s cell wall causing it to die. There are even some based on natural plant products such as peppermint oil. Whilst it can be argued that good hygiene will outperform an antimicrobial-treated textile, there are studies which show that antimicrobials reduce things such as odour (no more perma-stink gym kit). It’s also been shown that people only wash most clothes because of odour and not soiling, so if the odour is minimised there is less need for washing and suppliers are claiming it lowers the carbon footprint.
- Insecticide/insect repellent finishes: For fabrics prone to insect attacks like silk and wool some people may choose to apply one of these finishes which will either drive the insects away (often Chrysanthemum based) or kill the insects. Whilst recognising that some insects are beneficial as pollinators it is also known that some insects such as mosquitos and ticks are disease-spreading vectors. Where mosquitos or ticks are likely to be encountered (mosquito nets and military clothing) it’s more common to have insecticides such as permethrin applied. Carrington Textiles has recognised the risks associated with permethrin and we have been working in conjunction with machinery suppliers to develop a process which applies the chemical only to the outside face of the fabric. There is no point in applying the chemical to the inside, this face is also next to the skin so with our technique the wearer gets a product which is active where it needs to be and is chemically clean next to their skin. Visit our UK Factory Pincroft’s website for more information on our precision spray technology.